Customized Skills Development
The legacy of solid Productivity training and certification experience: actionable, Proven, Results-Oriented customized training programs are tailor-made to meet a wide range of training needs. Productivity Innovation delivers specific training events in Operational Excellence and Innovation to help companies go beyond mere Lean tools and build a growth path: Lean in Support Services, Lean in Laboratories and R&D, Leading Lean and Operational Excellence, Customer Centricity, and building a Zero Failure strategy.
Our programs range from Leadership and Executive Awareness programs to on-the-job training for Operational Teams, in both Industry and Services. We offer classroom training, but also practical workshops, modular curriculum training over a period of several months, and of course regular support in the implementation. Our programs can be customized to fit different manufacturing, service, and healthcare environments.
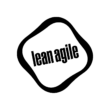
Lean Leader Certification
For companies that want to build solid internal improvement capabilities, we provide in-house customized education and certification programs to create or reinforce the skills of their Process Improvement Managers.
Learn more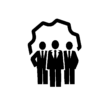
Lean leadership and constructing a lean management system
Lean Management System, Leadership, Gemba Walks, Leadership Standard Work: The success of a lean initiative depends on actively engaging leaders at every level in the organization. This session explores the need to develop a system for managing lean initiatives.
Learn more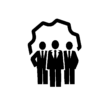
Lean Manager Support and Coaching
We act as sensei, and provide support and coaching to newly graduated Lean Managers to enhance their success in the transformation journey.
Learn more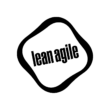
Lean Transformation
Lean transformation, Lean Services, Lean Management, Lean Marketing, Lean in HR: In this session, we explore how lean transformations occur in service organizations.
Learn more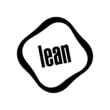
Managing flows in a service environment
Visual management, performance management, lean services: The main difference between manufacturing and services is Visibility.
Learn more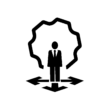
Performance management and key performance indicators
Performance management, KPIs, Metrics, and Leadership: In this session, we examine key performance indicators, including customer satisfaction, response time, right first time (%), on-time delivery (%), and productivity.
Learn more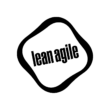
Programming and scheduling service flows
Flow management: Discover different ways of scheduling activities according to specific features of flow and demand.
Learn more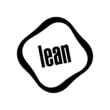
Value Stream Analysis
Value Stream Mapping, Value Stream management: In this session you will learn how to scrutinize steps and data uncovered during value stream mapping and find the weaknesses within an organization.
Learn more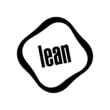
Value Stream Mapping
Flow Management: Visual management lies at the heart of Lean. In this session we take an in-depth look at the importance of making activities visible, and the development of a visual system that allows managers and team members to manage their activities and monitor performance.
Learn more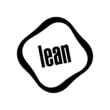
Visual Management
Value Stream Mapping, Value Stream management: This session presents a step-by-step methodology for value stream management (VSM)—the cornerstone for planning lean activities in all processes.
Learn more