Area of interest: Guiding Transformation
– Available Training Formats:
We provide Overview sessions, Practical workshops, Training seminars (with certificates), and customized Lean certification programs.
Learn more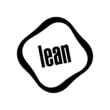
Developing a Problem Solving Culture
5 Why's, A3: During the lean transformation process, teams inevitably encounter problems that need to be solved before additional progress can be made. Equipping your team members with quick and easy-to-use problem-solving tools enables them to tackle issues as they arise.
Learn more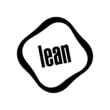
Hoshin-Kanri - Policy Deployment
Hoshin Kanri is the structured approach of Policy Deployment and Strategy Deployment: Guided by lean case studies, our sessions teach you how to align corporate objectives with workplace activities and day-to-day operations.
Learn more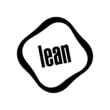
Introduction to lean principles and waste
Waste, Lean, Value: This module will introduce the fundamental principles of Lean in a service environment.
Learn more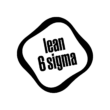
Introduction to Six Sigma
Implementing a Lean workflow requires reducing process variation. Six Sigma is a project management and problem-solving method based on the analysis of statistical data and aimed at reducing defects and variability.
Learn more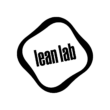
Lean in laboratories
Laboratories are critical for many industries: pharmaceutical, food, chemical industries. From the control of raw materials to the quality control and validation of semi-finished or finished products for batch release, laboratories are critical in the Value Chain.
Learn more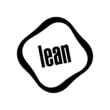
Lean in R&D
From the approval of product evolution to the development of new products and services, the work of R&D is essential for a company’s growth. In this session we look at how to bring lean techniques to R&D and Engineering departments.
Learn more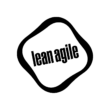
Lean Transformation
Lean transformation, Lean Services, Lean Management, Lean Marketing, Lean in HR: In this session, we explore how lean transformations occur in service organizations.
Learn more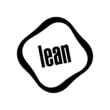
Managing flows in a service environment
Visual management, performance management, lean services: The main difference between manufacturing and services is Visibility.
Learn more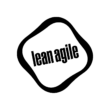
Programming and scheduling service flows
Flow management: Discover different ways of scheduling activities according to specific features of flow and demand.
Learn more