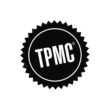
A ZERO FAILURE STRATEGY/BEYOND THE TOTAL PRODUCTIVE MAINTENANCE PILLARS
Productivity Innovation and Productivity Latin America
This Virtual two-day program will help leaders understand the organic development of a Zero-Failure Strategy. It has been developed based on more than 30 years of experience supporting companies in TPM implementation. Since the world has changed, everything must change. You will understand the Tree of Industrial Excellence and how solid foundations are driving your organization to the path of Zero Failure!
Register nowPROGRAM DESCRIPTION
If your value-streams are capital equipment intensive, developing an internal Total Productive Maintenance (TPM) resource will help you eliminate the equipment reliability issues—breakdowns, minor stops, long changeover adjustments, and other inefficiencies—that are hurting your competitiveness.
When moving from 40% OEE to 85% OEE you can double your capacity with no capital investment. And that’s just one benefit of successful implementation of Total Productive Maintenance (TPM), other gains include:
Technical benefits such as…
- Productivity improvement of more than 35%.
- Increased equipment effectiveness from 50-70% to 80-90%.
- Unplanned downtime (breakdown & minor stoppages, etc.) reduced by about 80%.
- Reduced quality defects by up to 50%.
- Scrap reductions of approximately 65%.
Social benefits such as…
- Motivated workers committed to improvement.
- Goal oriented efficient teams.
- Pro-active, solution oriented thinking and acting.
- Safe and stable operating environment.
Equipment and process reliability are too important to your business success not to have a TPM effort and a well-trained TPM Manager to guide the implementation.
This highly interactive, fully accredited program is designed for corporate and plant personnel looking to learn, launch, and lead a proven, systemic, equipment and maintenance management improvement process—Total Productive Maintenance (TPM). Combining classroom learning with simulations, group exercises, targeted discussion sessions, and shopfloor application, TPM practitioners deep dive the concepts and tools of TPM and share lessons from their implementation experiences.
Participants learn how to establish the daily management behaviors that will sustain TPM
and ensure alignment with overall improvement and Environmental, Health, and Safety goals.
Fully accredited certification for TPM managers and reliability leaders since 2010.
Over four non-consecutive weeks, attendees participate in a series of learning modules focused on the three critical areas for success: Planning, Doing, and Leading.
Between session weeks on the campus of The Ohio State University’s, students implement TPM projects at their own companies and present results during the next session week.
PROGRAM OBJECTIVES
TPMC graduates will gain overall knowledge of the eight pillars of TPM and will be able to:
- Establish and customize a strategy for implementing TPM
- Properly use machine performance data to identify and execute a tactical action plan
- Justify and implement a complete maintenance planning and scheduling process
- Conduct and lead autonomous maintenance kaizen events
- Design and perform site-specific TPM auditing processes
- Establish a baseline data collection process and understand how to use the OEE metric
- Conduct breakdown analysis reviews, and grasp their importance
- Organize and control spare parts
- Use the principles of Early Equipment Management