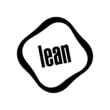
Managing flows in a service environment
Visual management, performance management, lean services: The main difference between manufacturing and services is Visibility.
Contact usMake it visible! This is the starting point for managing flow in a service environment. In a manufacturing workplace, it is easy to see machines running and material moving, but in a typical service environment, all you can see are people and computers. It is difficult, if not impossible, to see at a glance what people are doing and how activities flow for the customer.
In this session, we introduce an effective visual flow management and visual performance measurement system and the related team routines necessary to uncover and eliminate waste in your current processes.
AVAILABLE FORMATS:
- Workshop: classroom learning, case study
- Facilitated Coaching/Consulting: implementation in your environment
Customized Skills Development
Learning by doing
The legacy of solid Productivity training and certification experience: actionable, Proven, Results-Oriented customized training programs are tailor-made to meet a wide range of training needs.
Productivity Innovation delivers specific training events in Operational Excellence and Innovation to help companies go beyond mere Lean tools and build a growth path: Lean in Support Services, Lean in Laboratories and R&D, Leading Lean and Operational Excellence, Customer Centricity, and building a Zero Failure strategy.
Our programs range from Leadership and Executive Awareness programs to on-the-job training for Operational Teams, in both Industry and Services. We offer classroom training, but also practical workshops, modular curriculum training over a period of several months, and of course regular support in the implementation. Our programs can be customized to fit different manufacturing, service, and healthcare environments.