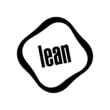
Developing a Problem Solving Culture
5 Why's, A3: During the lean transformation process, teams inevitably encounter problems that need to be solved before additional progress can be made. Equipping your team members with quick and easy-to-use problem-solving tools enables them to tackle issues as they arise.
Contact usBecause problems come in all sizes, you need a variety of techniques in your problem-solving arsenal. This session explores in-depth A3 thinking and A3 implementation:
- how to make an effective problem statement
- how to use Root Cause Analysis techniques such as 5 Why’s, Fishbone Diagram,
- how to measure the benefits of an effective problem solving.
AVAILABLE FORMATS
- Workshop: classroom lecture, case study
- Facilitated Coaching/Consulting: implementation in your environment
Customized Skills Development
Learning by doing
The legacy of solid Productivity training and certification experience: actionable, Proven, Results-Oriented customized training programs are tailor-made to meet a wide range of training needs.
Productivity Innovation delivers specific training events in Operational Excellence and Innovation to help companies go beyond mere Lean tools and build a growth path: Lean in Support Services, Lean in Laboratories and R&D, Leading Lean and Operational Excellence, Customer Centricity, and building a Zero Failure strategy.
Our programs range from Leadership and Executive Awareness programs to on-the-job training for Operational Teams, in both Industry and Services. We offer classroom training, but also practical workshops, modular curriculum training over a period of several months, and of course regular support in the implementation. Our programs can be customized to fit different manufacturing, service, and healthcare environments.